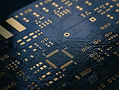
Reliability of technology

Within our THT (Through-Hole Technology) services, we combine traditional skills with the latest innovations in manufacturing processes to ensure the highest possible quality for printed circuit boards. This technology has long been the industry standard and is still a key component in many electronic products, especially where robust electrical connections and high mechanical strength are required. Our production line for THT is equipped with modern automated machines that enable precise insertion of components through the openings of the printed circuit board and ensure high-quality soldering.
Visual control and precision production
MANUAL OR AUTOMATED PLACEMENT
We produce printed circuits with a manual or automated method of inserting THT components for subsequent wave or selective soldering, where the selected process is adapted to the specifics of the circuit or customer requirements. We ensure that the components are correctly inserted and sealed, which gives the products the necessary strength and durability.



Advanced soldering processes
HIGH-QUALITY SELECTIVE SOLDERING
Our THT component soldering technology is complemented by advanced roller and selective soldering processes, which enable precise and uniform soldering on every joint. This ensures that all electrical connections are strong and reliable, which is especially important in applications that require high durability and long-term reliability.
Technological suitability ensures progress
Technology is always in the first place for us. That's why we have in our machine park both a machine for the dimensional pre-preparation of THT components. Polyver NCG, and soldering machines from the ERSA manufacturer which enable us to perform wave and selective soldering. So we can fulfil even high expectations and meet the customer requirements for the specific and high-quality production of electronic circuits.
Wave soldering is a bulk soldering process used fort he manufacturing of printed circuit boards. The circuit board is passed over a pan of molten solder in which a pump produces an upwelling of solder that looks like a standing wave. As the circuit board makes contact with this wave, the components become soldered to the board. Wave soldering is nowadays used for large power devices and high pin count connectors.
